What are Aerospace Composites?
Updated September 2023
Composite materials are formed by combining at least two different materials on a macroscopic scale to produce a resultant material with properties that are a blend of the component material properties. “Composites” is a broad term referring to a wide range of materials, but as used in this article, the term refers to fiber-reinforced polymer composites, specifically carbon fiber, glass fiber, and aramid fiber combined with epoxy.
Aerospace composites are a subset of composite materials that are suitable for use in aircraft and spacecraft applications. What differentiates aerospace composites from the rest of the field of composite materials is the strength, weight, and
quality standards of aerospace composite materials as well as the regimented procedures used to design, manufacture, and test aerospace composite structures. Additionally, the material properties and process variables of aerospace composites are quantified and tightly controlled. Although the focus of this article is primarily on aircraft applications, the information and techniques could just as well be applied to other high performance structures in race cars, sailboats, electric vehicles, or spacecraft.
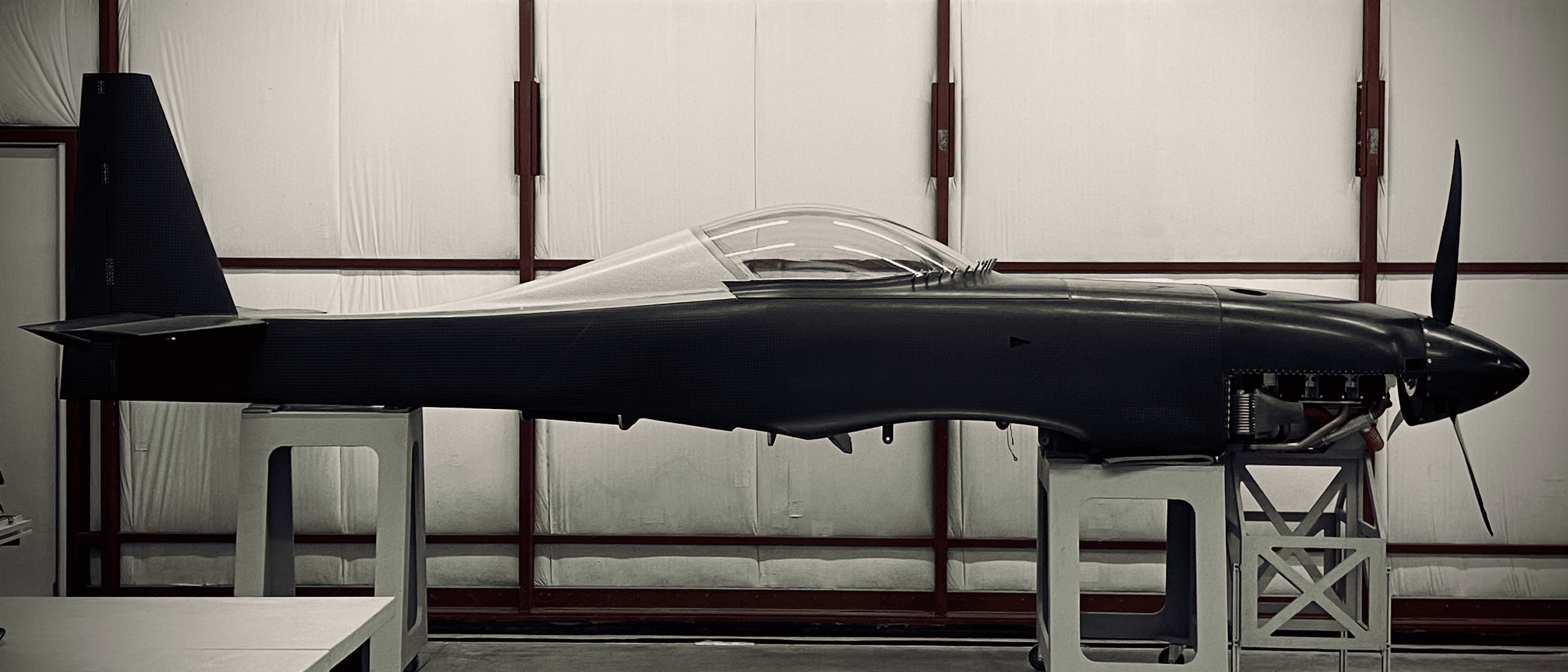
Why Use Composite Materials?
Composite materials offer many advantages in aircraft applications when compared to conventional materials such as metals. Increased strength, increased stiffness, reduced weight, reduced part count, and longer lifespan through greater fatigue limits and better corrosion resistance are benefits that can be achieved by replacing metals with composites. Composite materials are quite versatile since their physical and mechanical properties can often be customized or “tuned” for an application by adjusting the composition of the specific material. The use of composites also opens up more options for the design geometry of aircraft structures since they are particularly well suited for compound curves and organic shapes such as engine cowlings, wheel fairings, and wing tips. When properly applied, all of these advantages translate into higher performance for an application. Aircraft that can fly higher, faster, and farther while carrying greater payloads are made possible through the use of composite materials. Many of the advancements that have occurred in aerospace over the past several decades have been made possible through the adoption of composite materials.
What are Fiber Reinforcements?
The major component of composite materials is the fiber reinforcement. The fiber reinforcement provides strength and stiffness in the direction that the fibers are aligned. The three most common fiber types found in aerospace applications are carbon fiber, glass fiber, and aramid fiber. These fiber types have different chemical compositions at the molecular level that generate different physical and mechanical properties at the macroscopic fiber level. Important properties of fibers include their strength, stiffness, toughness, temperature capability, density, conductivity, chemical compatibility, fatigue life, and cost.
What is Carbon Fiber?
Individual carbon fiber filaments are composed of 93%-95% carbon atoms, which gives the fiber its characteristic black color. Carbon fiber can be derived from three polymer precursors that include polyacrylonitrile (PAN), rayon, and pitch. The most common polymer precursor is PAN. There are several chemical and mechanical processes required to convert the polymer precursor into strands of carbon fiber. Summarizing at a high level, PAN is mixed with other raw materials and then spun into fibers. From there, the fibers are chemically altered to stabilize bonding. These fibers are then heated to high temperatures causing nearly all non-carbon atoms to be expelled, leaving behind tight carbon crystalline structures. At this point, the fibers are treated with coupling agents to improve their ability to bond with resins. The individual fiber filaments are only 5 to 10 microns (0.0002 to 0.0004 inches) in diameter. They are combined into tows consisting of fiber bundles ranging from 1,000 (1k) to 320,000 (320k) individual fibers.
Carbon fiber is one of the most universally recognized types of fiber reinforcement. The development of carbon fiber, in the form commonly known today, began in the early 1960’s with the first high performance fibers entering the market shortly after in aircraft and spacecraft applications. Over many years of experimenting with different manufacturing processes and deriving it from different base materials, the strength of carbon fiber has greatly improved along with its versatility as an end-use product. It is important to note that not all carbon fiber is created equal. There are many different carbon fiber types with ranging values of strength, stiffness, and cost.
Physical Characteristics
Carbon fiber is a versatile material providing an excellent balance of high strength, high stiffness, low density, and moderate pricing compared to glass and aramid fibers. It is mildly conductive of electricity but highly conductive of heat along the length of the fiber. Carbon fiber filaments as a reinforcement material have extremely high temperature capability. Carbon fiber is dimensionally stable over a broad range of temperatures and has a low coefficient of thermal expansion.
Best Use Applications and Limitations
The high strength-to-weight ratio of carbon fiber makes it well suited for a wide variety of aerospace applications ranging from airframe structures to spacecraft heat shields. Outside of aerospace applications, carbon fiber can be found in boats, race cars, and sports equipment. One of the drawbacks of carbon fiber is its conductivity, which makes it difficult to combine with certain metals because it creates a potential for galvanic corrosion. Its conductivity also makes it a poor choice for applications where communication signals are required to pass through it, such as antenna enclosures or radomes. When it comes to small, detailed geometries, carbon fiber is often not the best choice. Small parts with features at dimensional scales approaching the size of fiber bundles are difficult to create with the range of fiber orientations necessary to attain desirable strength characteristics.
Manufacturability
Raw carbon fibers can be cut with simple cutting tools. When combined with resin in composite form, carbon fiber is best cut with diamond coated tools that grind rather than creating chips. Removal of heat is critical while cutting to prevent thermally damaging the resin matrix that holds the carbon fibers together. Carbon fiber dust is conductive, and it can interfere with or damage electronics with exposed circuitry. If enough carbon dust collects on electrical hardware, it can cause an electrical short that can lead to a full electrical component failure. Exposure to carbon fiber dust should be limited as it can be irritating to skin, eyes, and lungs.
Learn More
If you’d like to learn more about how to consistently make high-quality composite parts and get hands-on experience working with carbon fiber, consider enrolling in one of our courses:
Aerospace Composites CourseAerospace Mold Making CourseThe courses are structured as a mix of both classroom lessons and hands-on demonstrations in the shop. Composite material fundamentals, design methods, material and process selection, and design for manufacturability are covered in class. Examples specific to student applications are used to immediately apply what is learned. Online versions of both courses are available as well at the links below:
Aerospace Composites Online CourseAerospace Mold Making Online Course